
PROCESS
Lean Competency System
Developed by Cardiff University, the Lean Competency System (LCS) provides a structured, externally accredited framework for building continuous improvement capability.
Improve business performance
Develop internal capability
Align training to strategy
Achieve recognised accreditation
Driving strategic change and continuous improvement

Developed by Cardiff University, the Lean Competency System (LCS) provides a structured, externally accredited framework for building continuous improvement capability.
Aligning with LCS ensures measurable business impact – you can expect to benefit from enhanced workforce engagement, stronger problem-solving capabilities, and sustained operational excellence.
Who should attend?

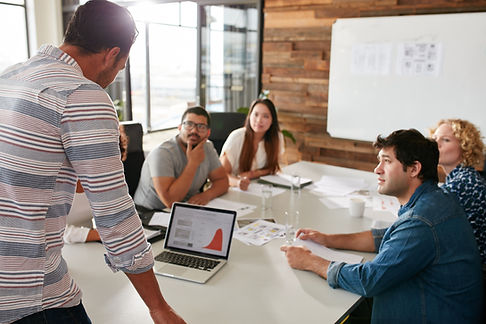
These accreditations are ideal for:
01.
Continuous Improvement Essentials (LCS Level 1a) – All employees, especially those new to Lean. Develops foundational knowledge to support and engage in improvement activities.
02.
Continuous Improvement Practitioner Programme (LCS Levels 1b and 1c) – Team leaders, supervisors, and managers actively involved in identifying, analysing, and implementing process improvements.
03.
Advanced Lean Coach Programme (LCS Level 2a) – Senior managers, Lean practitioners, and continuous improvement (CI) leaders looking to coach teams, drive cultural change, and lead strategic Lean transformations.
Accreditation structure
Developed by Cardiff University, the Lean Competency System (LCS) provides a structured, externally accredited framework for building continuous improvement capability.
01
Continuous Improvement Essentials (LCS Level 1a)
The Continuous Improvement Essentials course provides participants with a foundational understanding of Lean principles and the importance of a CI culture within an organisation. It explores the core principles of CI, why they matter, and how they drive operational excellence.
Aligned with the LCS Level 1a certification, this course helps individuals develop the awareness and basic problem-solving skills that are essential for supporting improvement activities.
Course structure
This one-day course is structured to provide a balanced mix of theory, discussion, and practical exercises.
-
Introduction to continuous improvement
-
Understanding Lean principles and CI methodologies
-
Exploring the importance of structured improvement approaches.
-
-
Identifying and eliminating wast
-
Introduction to the eight wastes and how to identify them
-
Hands-on application of process mapping and waste reduction techniques.
-
-
Problem-solving tools and techniques
-
Overview of structured problem-solving methodologies.
-
Practical use of basic CI tools such as 5S, PDCA, and visual management.
-
-
Embedding CI into daily operations
-
Understanding the role of visual management and performance tracking.
-
Developing an action plan to apply CI concepts in the workplace.
-
Certification requirements
-
Completion of the one-day training.
-
Demonstration of understanding through engagement in practical exercises.
02
Continuous Improvement Practitioner Programme (LCS Levels 1b and 1c)
This five-day programme is structured to cover theory, hands-on exercises, and workplace application.
-
Lean fundamentals and process mapping
-
Understanding Lean principles and CI frameworks.
-
Developing process maps to identify inefficiencies and prioritise improvements.
-
-
Identifying and reducing waste
-
Applying waste reduction techniques, including value stream mapping and flow analysis.
-
Hands-on experience in eliminating non-value-added activities.
-
-
Problem-solving and root cause analysis
-
Using structured problem-solving techniques such as A3, 8D, and DMAIC.
-
Applying cause-and-effect analysis, ‘5 Whys’, and FMEA.
-
-
Leading CI projects and change management
-
Planning, leading, and sustaining improvement initiatives.
-
Learning strategies to engage teams and drive cultural change.
-
-
Embedding continuous improvement
-
Implementing visual management and performance measurement techniques.
-
Developing standard work and leader standard work practices.
-
Certification requirements
-
Completion of the five-day training.
-
Application of Lean tools to an improvement project.
03
Advanced Lean Coach Programme (LCS Level 2a)
The Advanced Lean Coach Programme is designed for experienced Lean practitioners and leaders seeking to enhance their coaching skills, deepen their knowledge of Lean transformation, and lead complex improvement initiatives.
Aligned with the LCS Level 2a certification, this course equips participants with the ability to coach, mentor, and embed Lean thinking across all levels of the organisation.
Course structure
This six-day programme is delivered in three two-day sessions, allowing for practical application between workshops.
-
The role of a Lean coach
-
Understanding the responsibilities and impact of a Lean coach.
-
Developing coaching styles that foster engagement and accountability.
-
-
Advanced problem-solving and facilitation
-
Applying A3 thinking, 8D, and DMAIC methodologies.
-
Using advanced facilitation techniques to support problem-solving teams.
-
-
Strategic deployment and Lean leadership
-
Learning how to align Lean coaching with organisational strategy.
-
Understanding Hoshin Kanri and its role in Lean transformation.
-
-
Cultural change and sustaining Lean practices
-
Embedding Leader Standard Work to ensure the sustainability of improvements.
-
Coaching leadership teams to create a CI culture.
-
Certification requirements
-
Completion of the six-day training.
-
Demonstration of coaching effectiveness through project application.
Looking for a public workshop?
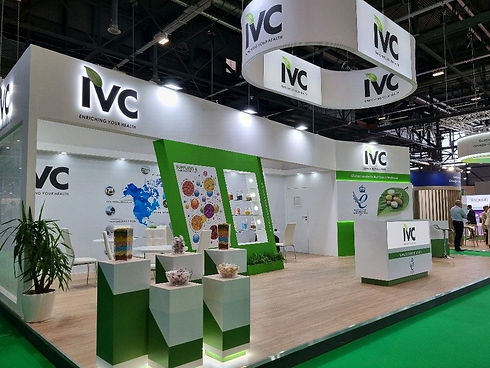