
Manufacturing glossary of terms
Unlock the secrets of manufacturing with our glossary of terms developed over 40 years by George Donaldson, Shingo Prize recipient! Take a deep dive into industry jargon. Don't wait! Master your industry knowledge NOW!
The story of how this glossary was created and has evolved, in the words of author George Donaldson.
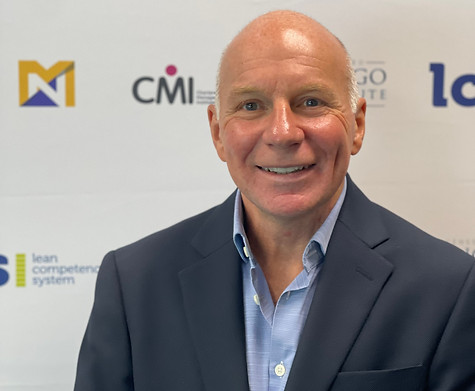
This glossary’s roots began in 2010 when I worked with Newsprinters Eurocentral Ltd. I noticed less emphasis on the practice and principles of Organisational Excellence in manufacturing and more on the language used to describe them.
Of course, people then became concerned about learning vast amounts of new words rather than paying attention to what they meant. Many terms also came about in the 1950s, and their original definitions weren’t applicable today. What we needed was a single reference point – a glossary. So, that’s what I created.
As I moved away from Newsprinters Eurocentral Ltd and worked with other businesses, I expanded the glossary to include all models and other tools and techniques. I was teaching courses in Continuous Improvement and realised manufacturing needed to be demystified; students were often overwhelmed with various acronyms.
Then, as manufacturing became about more than just improvement – and about leadership, management, and psychology too – the glossary grew once more. It now includes theories from the likes of Maslow, Herzberg, and McGregor, and even modern theorists such as Sinek. I’ve also included the GROW model to reflect manufacturing’s focus on developing people through coaching and mentoring.
Manufacturing is much more holistic today. And this glossary echoes that. Sitting at over 300 definitions, you’ll be able to find any term you need to achieve Organisational Excellence in the modern world.
Good luck on your journey.
George Donaldson
Term:
8 Principles of Quality Management
What started with Dr Deming’s 14 Management Principles was introduced into ISO as the fundamental principles for all ISO Standards.
These principles, if achieved, would on their own, make a company world class:
Customer focus.
Leadership.
Involvement of people.
Process approach.
Systems approach to management.
Continual improvement.
Factual approach to decision making.
Mutually beneficial supplier relationships.
Term:
80−20 Rule
Vilfredo Pareto’s 80−20 Rule was originally developed to prove that 80% of Italy’s wealth was distributed amongst 20% of its people.
It quickly transcended into many other contexts, specifically in the field of engineering and problem solving. For example, 80% of failures are caused by human error and 20% by equipment failure.
Term:
8D
8D are the eight disciplines for effective problem solving.
Originally known as team orientated problem solving (TOPS), it was developed and introduced in the 1980s by the Ford Motor Company.
The eight disciplines were developed by Ford to ensure that integrated teams were created to solve problems.
At the Manufacturers Network, we have integrated the 8D philosophy into our own problem solving, FMEA and SMED processes:
Create the team.
Implement interim action.
Define the problem (see 5W–2H).
Perform RCA (see RCA).
Determine the best solution.
Use the PDCA cycle (see PDCA).
Set the standards (see setting standards).
Sign-off and celebrate.
Term:
A3 Process
The A3 Process was developed by Toyota as a communications tool to ensure that only the key (vital few) facts are communicated to all relevant staff and specifically, to reduce the need for PowerPoint presentations.
This method ensures that all the relevant information for problems, projects and processes are detailed and communicated on a single A3 size piece paper (11 x17).
At the Manufacturers Network, we have integrated the A3 process into our problem solving, SMED and FMEA templates.
Term:
ABC Analysis
Purpose of the ABC Analysis: the business goal is to have on time delivery while minimising inventory expense:
A. These items typically have high value and are 80% of inventory costs.
B. These items typically have a mid-range cost and constitute 15% of inventory costs.
C. These items are less important and constitute 5% of inventory value.
By closely managing A and B items (50% of the stock keeping units), we can control 95% of the inventory cost.
Term:
Absenteeism
Absenteeism can be defined as any absence from work that extends beyond what would be considered reasonable and customary due to vacation, personal time, or occasional illness.
Term:
Adair’s Action Centred Leadership
John Adair, a British academic and leadership theorist, authored more than forty books (translated into eighteen languages) on business, military, and other leadership.
Adair’s Action Centred Leadership model describes leadership in terms of three interlocking or overlapping elements of responsibility and concern, highlighting the relationship between them:
The needs of the task.
The needs of the team.
The needs of the individual.
These three elements should be the main focus of leadership and therefore, should be constantly considered: achieving the common task; developing and meeting the needs of individual team members; and building and maintaining the team. If all three elements are satisfied, then the team becomes effective, achieving the required results.
Term:
Affinity Diagram
The Affinity Diagram is a problem solving technique used to capture large amounts of ideas, opinions, issues and causes. It organises them into natural categories/groups based on their relationship (unlike the cause-and-effect diagram that has pre-determined categories/groups).
Term:
Aims (Goals)
Business Aims, or Goals, are considered to be the long-term strategic goals that are set over 3−5 years and are deemed vital or critical in achieving the business vision.
Term:
Andon
Andon is part of the visual management system that is used to notify operators and managers when a problem occurs and when support/assistance is required. These can be activated manually (pull cord or button) or automatically (machine settings or sensors).
Term:
Aspects and Impacts
Used in ISO 14001 as the main planning element, Aspects and Impacts help determine how the aspects of our work/job and the products or services for the company impact the environment.
Using our Aspects and Impacts assessment templates, we can RAG rate the impacts to better prioritise those that we can control and improve.
Term:
Asset Criticality
This is the process developed by the Manufacturers Network to RAG rate all of our equipment, activities and processes. The Asset Criticality process looks at what happens when it fails or goes wrong and what effect it will have on:
Safety and legal.
Hygiene.
Availability.
Performance.
Quality.
Reliability.
Maintainability.
Environment.
Cost.
SPF - single point of failure.
Term:
Audit
A systematic and independent examination to determine whether quality activities and related results/outputs, including H&S and environmental impacts, comply with planned arrangements and whether those arrangements are effective and suitable to achieve objectives.
Term:
Availability
Availability of equipment means exactly that. Is the equipment available to use and produce quality products? This measure considers all unplanned downtime losses.
Term:
Baguley’s Four Main Teams
Phil Baguley was an author and management consultant in the UK and mainland Europe.
Through his research, Baguley identified Four Main Teams and describes their purposes foundin organisations.
Teams which provide management or control of activities:
Senior management/leadership team oversees or co-ordinates activity on an ongoing and continuous basis. Sets direction and activities of the organisation.
Specific project teams to oversee time limited projects.
Teams which make something:
Production teams.
Teams which do something:
Sales.
Finance.
Marketing.
Customer service.
Teams which evaluate or make recommendations:
Problem solving.
Continuous improvement.
Today, we can describe many other organisational teams, such as cross functional teams, permanent teams, functional teams, virtual teams, group teams, Kaizen teams.