Introduction To Lean Continuous Improvement: A Primer
- Mark Leeson
- Sep 7, 2023
- 3 min read
Updated: Nov 20, 2023
Lean Continuous Improvement is a business philosophy that’s all about maximising value while minimising waste, initially emerging from the manufacturing sector.
Staying relevant and efficient is paramount for success. And Lean Continuous Improvement provides organisations with the tools they need to thrive in a rapidly changing landscape.
Transitioning to a Lean business model involves leadership commitment, employee training, value stream analysis, and Lean tools to cultivate a culture of perpetual improvement.
In this blog, we’ll take a look at the key principles (like Kaizen and Respect for People) and tools (such as Value Stream Mapping and the PDCA cycle) that foster systematic problem-solving and waste elimination.
Foundations of Lean thinking
Lean thinking is a mindset to streamline processes and improve productivity – ultimately, to deliver more with fewer resources.
Lean Continuous Improvement encourages a culture of efficiency and innovation through continuous small, incremental changes to create sustainable organisational growth, efficiency, and customer satisfaction.

Lean basics
Lean thinking, often referred to simply as “Lean,” is relevant to many industries, including healthcare, software development, and service sectors. It’s a mindset that encourages organisations to streamline processes, improve productivity, and enhance overall customer satisfaction.
The primary goal of Lean is to deliver more value to customers with fewer resources. To achieve this, organisations must identify and eliminate non-value-added activities, reduce lead times, and create a culture of Continuous Improvement.
Principles of Lean Continuous Improvement
Continuous Improvement is a fundamental aspect of Lean thinking. It’s not a one-time project or a set of tools but a holistic approach following key Lean Continuous Improvement principles…
Kaizen
In essence, Kaizen (meaning “change for the better”) embodies the belief that even the most modest adjustments, when consistently applied, can substantially enhance processes, productivity, and overall organisational performance.
It empowers individuals to take ownership of their work, fostering a culture of innovation and a shared commitment to constant progress.
Organisations can tap into the collective power and creativity of their workforce and also pave the way for sustained transformation.
Respect for People
People are at the core of any organisation. In the context of Lean, the principle of “Respect for People” underscores the paramount importance of valuing employees’ knowledge, ideas, and contributions. When individuals within an organisation feel respected and empowered, they become catalysts for meaningful and sustainable improvements.
Recognising and nurturing the potential of every team member not only enhances their job satisfaction but also fuels collaboration and innovation.
Value stream mapping
A powerful tool, value stream mapping is a visual technique widely employed by Lean practitioners. Value stream mapping means meticulously identifying and eliminating wasteful elements within organisational processes. It serves as a navigational blueprint, allowing organisations to gain deep insights into the flow of value creation across their operations.
PDCA Cycle
The Plan-Do-Check-Act (PDCA) – also known as the Deming Cycle or the Shewhart Cycle – encourages a systematic approach to problem-solving and improvement. It means identifying and resolving issues holistically – providing a structured framework for sustainable improvements that are continuously refined.
Plan: Identifying problems, setting clear goals, and outlining the strategies and resources required.
Do: Putting the strategies into practice and implementing changes.
Check: Evaluating the results of the actions taken and comparing them to the initial goals and performance metrics.
Act: Making informed decisions based on the evaluation – if the results meet the objectives, organisations may choose to adopt the changes. However, if there are discrepancies or shortcomings, organisations may restrategise.
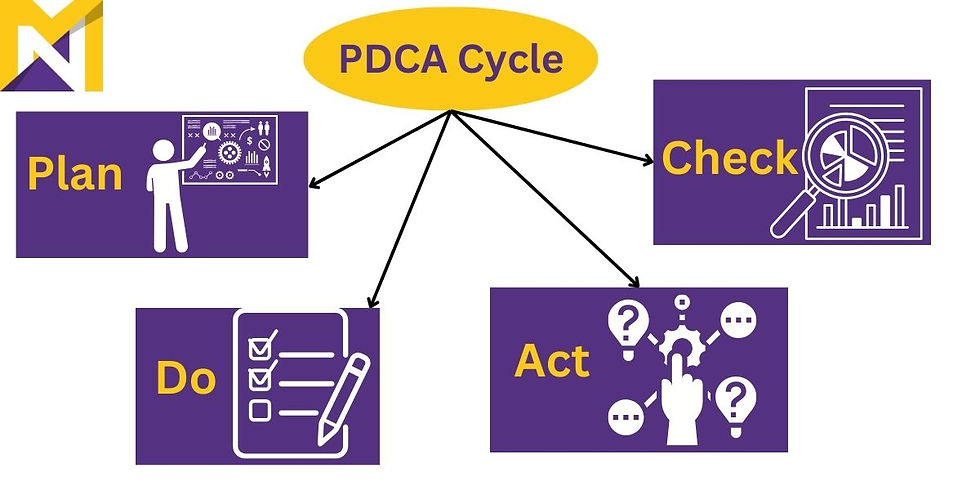
Just-in-Time (JIT)
Just-in-Time (JIT) is a fundamental Lean principle designed to optimise production and service delivery. The core objective of JIT is to produce and deliver products or services precisely when they’re required – minimising or even eliminating waste.
Transitioning to a Lean business model
Transitioning to a Lean business model can be a significant undertaking, but it can be done with:
Leadership commitment: Lean transformation begins at the top. Leaders must be committed to the process, set clear expectations, and lead by example.
Education: Employees need to understand Lean principles and tools, with the right education and training to develop the necessary skills.
Value stream analysis: Identify the value streams within your organisation to uncover inefficiencies.
Implement Lean tools: Systemically apply relevant Lean methods and techniques, such as 5S, Kanban, and Total Productive Maintenance (TPM).
Continuous monitoring: Implement Key Performance Indicators (KPIs) to measure progress – and regularly review and adjust.
Cultural shift: Encourage a culture of Continuous Improvement where employees are engaged, empowered, and encouraged to contribute ideas for improvement.
Speak to Manufacturers Network
Lean Continuous Improvement Education is important and is a powerful approach that can transform businesses. By embracing Lean principles and fostering a culture of Continuous Improvement, organisations can optimise processes, reduce waste, and enhance customer value to stay competitive.
If you’re looking to take your business to the next level, start your Lean transformation with Manufacturers Network. For more information or to get in touch, you can reach us at 0161 533 1617 or send us an email at hello@manufacturersnetwork.co.uk.