Lean Kanban Systems: Streamlining Business Processes
- Mark Leeson
- Sep 13, 2023
- 4 min read
Updated: Jan 12, 2024
The Kanban system is a scheduling system for lean manufacturing to improve business
efficiency and streamline workflow management.
Organisations often turn to Lean tools and methodologies such as Value Stream Mapping, and 5 Whys to optimise their operations and among these tools, the Kanban system has emerged as a powerful technique to achieve continuous improvement and increased productivity.
In this article, we’ll explore the basics of the Kanban system, its Continuous
Improvement benefits, transformative impact on workflow management, and provide
practical tips for its implementation.
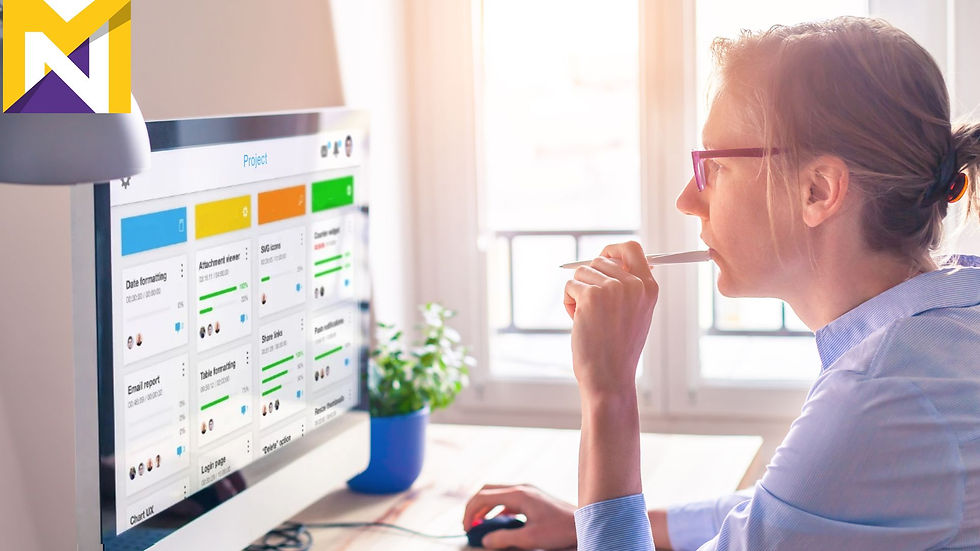
Basics of the Kanban system
The Kanban system, originating from Toyota’s manufacturing processes, has evolved
into a versatile tool used in various industries.
At its core, Kanban is a workflow management system that enables organisations to
visualise their work processes, identify bottlenecks, and enhance efficiency.
The fundamental principles of the Kanban system
● Visualising workflow: Kanban uses visual boards or cards to represent tasks or
projects. These cards move through different stages of a process, providing a
real-time snapshot of work in progress.
● Limiting work in progress (WIP): Set limits on the number of tasks that can be
in progress at any given time to prevent overloading resources and maintain a
steady workflow.
● Pull system: Kanban follows a pull-based approach, where work items are
pulled into the next stage of the process only when there is capacity, as opposed
to a push system where work is pushed onto resources regardless of capacity.
● Continuous Improvement: Kanban encourages a culture of learning and
adaptation by making issues visible and prompting teams to analyse and resolve
them.
Benefits of Kanban in Continuous Improvement
The Kanban system offers many benefits for organisations striving towards continuous
improvement:
● Enhanced efficiency: Kanban optimises workflow by eliminating bottlenecks
and reducing idle time, leading to improved overall efficiency.
● Increased productivity: By limiting WIP, teams can focus on completing tasks
before starting new ones, resulting in faster task completion and increased
productivity.
● Improved quality: Kanban’s visual cues and Continuous Improvement focus
help identify and address quality issues promptly, resulting in higher product
and service quality.
● Flexibility: Kanban is adaptable to different processes and industries, making it
suitable for a wide range of applications.
● Reduced lead times: The pull system reduces lead times and ensures that work
items are delivered more quickly.
Practical Tips for Implementation
Implementing Kanban successfully requires careful planning and execution. Here are
some practical tips to consider:
● Start small: Begin with a single team or process to pilot the Kanban system
before scaling it to your entire organisation.
● Provide training: Ensure that team members understand the principles and
mechanics of Kanban with training and workshops.
● Customise boards: Tailor Kanban boards to fit your specific workflow and
processes, making them as simple or detailed as needed.
● Regular reviews: Hold regular meetings to review progress, identify issues, and
make necessary adjustments.
● Continuous Improvement: Encourage a culture of continuous improvement by
using Kanban to identify and address process inefficiencies.
An example of Kanban streamlining…
Using Kanban to manage projects
Here’s a step-by-step example of how a manufacturing company can use Kanban to
manage its project…
1. You must first understand the current workflow for creating your Kanban board.
Identify the steps involved in the manufacturing process, from raw materials
procurement to finished product delivery.
2. You can use a physical board with sticky notes or a digital platform (like Trello or
Jira) to create your Kanban board. Add columns to represent different stages of your
manufacturing process – your first ones might include ‘To-Do,’ ‘In Progress,’ and ‘Done.’
3. Identify individual tasks within each project – these might be cutting, welding,
painting, quality control, and packaging. Each should be represented by a Kanban card,
which contains relevant information like the item description, priority, and due date.
4. Determine how many work items can progress at each stage of the workflow without
causing bottlenecks or overloading your team. WIP limits ensure that work flows
smoothly and resources are not spread too thin. Enforce WIP limits strictly.
5. Cards should move from left to right as work progresses through the workflow. Team
members should be able to see the current status of each task at a glance.
6. Use colour-coding or tags to prioritise each work item. This allows your team to focus
on the most critical tasks first and ensures that high-priority items are addressed
promptly.
7. Regularly review your Kanban board with your team. Discuss any bottlenecks or
issues that arise and collaborate on solutions. Continuous Improvement is a
fundamental aspect of Kanban, so be open to making adjustments to your workflow to
increase efficiency and quality.
8. As your manufacturing company gains experience with Kanban, consider expanding
its use to other departments or projects. Adapt and refine your Kanban system based on
the specific needs of your organisation.
By visualising their work in this manner, the team can efficiently manage their tasks, ensure a smooth workflow, and continuously improve their processes.
Learn more about Kanban
The Kanban system is a powerful tool for enhancing business efficiency and
streamlining workflow management. Its adaptability, visual nature, and focus on
continuous improvement make it an invaluable asset for organisations seeking to
optimise their processes and deliver high-quality results.
By understanding the basics of Kanban and implementing it effectively, businesses can
achieve greater productivity, reduced lead times, and improved overall performance.
If you would like more information about Lean Kanban Systems or would like to sign up
for one of our courses, please contact us:
● Phone: 0161 533 1617
● Email: hello@manufacturersnetwork.co.uk
● Or get in touch online.