The Power Of Continuous Flow In Lean Improvement
- Mark Leeson
- Oct 10, 2023
- 3 min read
Updated: Nov 15, 2023
Modern business and manufacturing companies are constantly searching for ways to improve efficiency, reduce waste, and enhance productivity.
At the heart of Lean Improvement, continuous flow is a powerful technique that can revolutionise work processes for Organisational Excellence. Read on to learn about the significance of continuous flow – and how to achieve it.
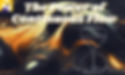
Understanding continuous flow
Continuous flow, also known as one-piece or single-piece flow, is a key principle of Lean improvement, emphasising the uninterrupted movement of materials, products, or information through a process. Unlike traditional batch processing, where large quantities are grouped and processed, continuous flow focuses on the steady and seamless progression of individual items from one stage to the next.
To illustrate this concept, let’s consider a manufacturing facility producing custom-made bikes. In a traditional batch production setting, workers might assemble ten bicycles at a time with various inefficiencies. If a problem arises with one item in the batch, it could delay the entire production line.
On the other hand, in a continuous flow system, each bicycle is assembled one at a time. As soon as one is completed, it moves to the next station for quality checks and so on, ensuring a smooth and uninterrupted workflow.
Benefits of streamlined work processes
Continuous flow in Lean improvement can positively impact an organisation’s performance – advantages include:
1. Productivity gains
Continuous flow minimises idle time and waiting periods, resulting in higher productivity levels. When work items move steadily through the process, there are fewer bottlenecks and less time wasted on setup or changeovers.
2. Reduced wastage
Lean processes, including continuous flow, aim to eliminate waste – i.e., overproduction, excess inventory, and unnecessary motion. This reduced waste not only saves resources but also reduces costs.
3. Improved quality
Continuous flow boosts the chances of immediately detecting and correcting defects or errors, as they’re less likely to be hidden within a large batch of work. This leads to higher-quality outputs and a decrease in rework or defects.
4. Faster delivery
Work streamlining with continuous flow means quicker delivery of products or services to customers, improving customer satisfaction and potentially gaining a competitive edge in the market.
5. Employee engagement
Continuous flow promotes a more engaging and less stressful work environment. Employees can see the immediate impact of their efforts, fostering a sense of ownership and pride in their work.
Steps to achieve continuous flow
Achieving continuous flow in Lean improvement requires careful planning, implementation, and ongoing monitoring.
1. Value stream mapping
Start by mapping the entire value stream to identify all the steps and processes to deliver your product or service. This visual representation helps pinpoint areas of waste and inefficiency.
2. Identify bottlenecks
Identify bottlenecks or constraints within the value stream where work tends to pile up and cause delays. Addressing bottlenecks is crucial for achieving continuous flow.
3. Standardise work
Develop standardised work procedures for each step in the process. Standardisation ensures consistent work and helps reduce variations that can disrupt the flow.
4. Reduce batch sizes
Gradually reduce batch sizes to transition from batch processing to continuous flow. This step may require changes in equipment, workstations, or layout to support smaller batches.
5. Implement visual management
Use visual management techniques, such as Kanban boards or Andon systems, to make the status of work items and the flow of materials and information easily visible to all team members.
6. Continuous Improvement
Continuous flow is an ongoing effort. Encourage a culture of Continuous Improvement within the organisation, where teams regularly review processes and make adjustments to further optimise flow.
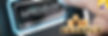
The power of continuous flow in Lean improvement: A real-life example
In a traditional manufacturing setup, the assembly process might involve grouping components into batches, resulting in longer production lead times and increased strain on both workers and equipment. However, by implementing continuous flow principles, the production line can ensure that each component is processed as soon as it arrives, without waiting for others to be completed.
The benefits are significant:
Reduced production lead times
Improved product quality
Enhanced worker morale
Optimised resource utilisation
This example highlights how continuous flow can revolutionise a dynamic manufacturing environment, enhancing both product quality and operational efficiency.
Continuous Improvement with Manufacturers Network
Continuous flow is a powerful tool to boost productivity, reduce waste, improve quality, deliver services faster, and increase employee engagement. By following a systematic approach and embracing Continuous Improvement, organisations can harness the power of continuous flow to drive efficiency and competitiveness.
To learn more about continuous flow in Lean improvement or sign up for one of our Lean courses, please contact us:
Phone: 0161 533 1617
Contact us online.