The Role Of 5S In A Lean Continuous Improvement Programme
- Mark Leeson
- Oct 3, 2023
- 3 min read
Updated: Nov 3, 2023
Lean methodologies empower businesses to streamline their processes, reduce waste, and enhance overall workplace efficiency. And among the tools and principles that Lean Continuous Improvement offers is the 5S framework. The 5S methodology is a systematic approach to workplace organisation and standardisation, emerging as a transformative Lean initiative. Integrating seamlessly with other Lean tools and techniques, such as Kanban and the 5 Whys Technique, the 5S methodology drives efficiency and Continuous Improvement.
This article will explore the significance of the 5S methodology within a Lean Continuous Improvement programme for businesses striving to achieve Organisational Excellence.

Defining the 5S methodology
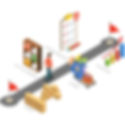
The 5S methodology is a structured approach rooted in Japanese principles. It serves as a powerful framework to cultivate an organised and highly efficient workplace environment.
What are the 5S principles?
1. Sort (Seiri)
Initially, organisations need to identify and remove unnecessary items from the workplace. This means sorting through tools, materials, and equipment to distinguish between essential and non-essential items. The goal is to create a clutter-free and organised workspace, which reduces the chances of errors and waste.
2. Set in Order (Seiton):
Next, the business needs to arrange and label items logically and systematically. Everything should have a designated place, making it easy for employees to locate tools and materials. Colour coding and labels can help promote consistency and efficiency.
3. Shine (Seiso):
Establishing cleaning routines and standards means the workspace remains tidy and well-maintained. A clean environment not only enhances employee morale but also reduces the risk of accidents or equipment breaking down.
4. Standardise (Seiketsu):
Creating and implementing standardised procedures and practises ensures that the organisation can sustain improvements over time – preventing clutter and inefficiencies from gradually returning.
5. Sustain (Shitsuke):
‘Sustain’ emphasises the importance of Continuous Improvement by fostering a culture of discipline and accountability – where employees are encouraged to adhere to the established standards and participate in ongoing improvement efforts. Regular audits and feedback mechanisms are crucial for sustaining Continuous Improvement.
Benefits of 5S in the workplace
The benefits of the 5S methodology align with Lean Continuous Improvement goals. They go beyond just tidying up the workspace but encompass a fundamental shift in the way an organisation operates and approaches its processes.
Enhanced efficiency: Systematically organising the workspace, arranging items logically, keeping workspaces clean and maintained, standardising processes, and sustaining these improvements can eliminate bottlenecks and time-wasting activities. This translates into faster production cycles, reduced lead times, and improved customer satisfaction.
Waste reduction: The 5S methodology identifies and removes unnecessary items and processes to reduce physical and non-physical waste. This not only saves money and resources but also frees up valuable workspace and mental capacity for employees to focus on value-adding tasks.
Improved safety: Clean and well-maintained workspaces contribute to a more pleasant and organised work environment and reduce the risk of accidents caused by clutter or unsafe conditions. A safer workplace means fewer disruptions and injuries, promoting continuous operations.
Employee engagement: When employees actively participate in sorting, organising, and maintaining their workspace, they become more invested in the success of Lean initiatives. This heightened engagement often leads to innovative ideas for further Continuous Improvement.
Quality improvement: Setting your workspace in order and standardising processes ensure that tools and materials are readily available – reducing errors and defects in processes. Moreover, standardised procedures enable the maintenance of a consistent level of quality across operations.
Cost savings: Lean practices are synonymous with cost savings. The 5S methodology can reduce excess inventory, wasted time, and expenses associated with accidents or inefficiencies, improving profitability.
Practical steps for 5S implementation

Implementing the 5S methodology in a Lean Continuous Improvement programme requires a structured approach:
1. Commitment from leadership:
You need commitment and support from top management for successful implementation.
2. Training and education:
Provide training to employees on the 5S principles and their significance in Lean and Continuous Improvement efforts.
3. Form cross-functional teams:
Create teams responsible for each of the 5S phases to drive implementation.
4. Sort (Seiri):
Identify and eliminate unnecessary items from the workplace. Ensure clear criteria for what stays and what goes.
5. Set in Order (Seiton):
Define storage locations and label items for easy identification. Visual management tools, like shadow boards, labels, and colour coding, can help.
6. Shine (Seiso):
Develop cleaning schedules and assign responsibilities. Conduct regular equipment maintenance to prevent breakdowns.
7. Standardise (Seiketsu):
Create standard operating procedures (SOPs) and work instructions, ensuring all employees understand and follow these standards.
8. Sustain (Shitsuke):
Establish a system of regular audits and self-assessment, encouraging a culture of Continuous Improvement and employee involvement.
9. Review and improve:
Continuously assess the effectiveness of 5S implementation. Make necessary adjustments and improvements as needed.
Discover the 5S methodology in a Lean Continuous Improvement programme
The 5S methodology plays a pivotal role in Lean Continuous Improvement to create a workplace that promotes efficiency, safety, and quality. When integrated into the culture of a Lean organisation, 5S becomes a driving force behind Continuous Improvement.
To learn more about the 5S methodology or sign up for one of our Lean courses, please contact us:
Phone: 0161 533 1617
Email: [email protected]
Contact us online