Understanding Lean Metrics And KPIs For Continuous Improvement
- Mark Leeson
- Sep 25, 2023
- 4 min read
Updated: Jan 11, 2024
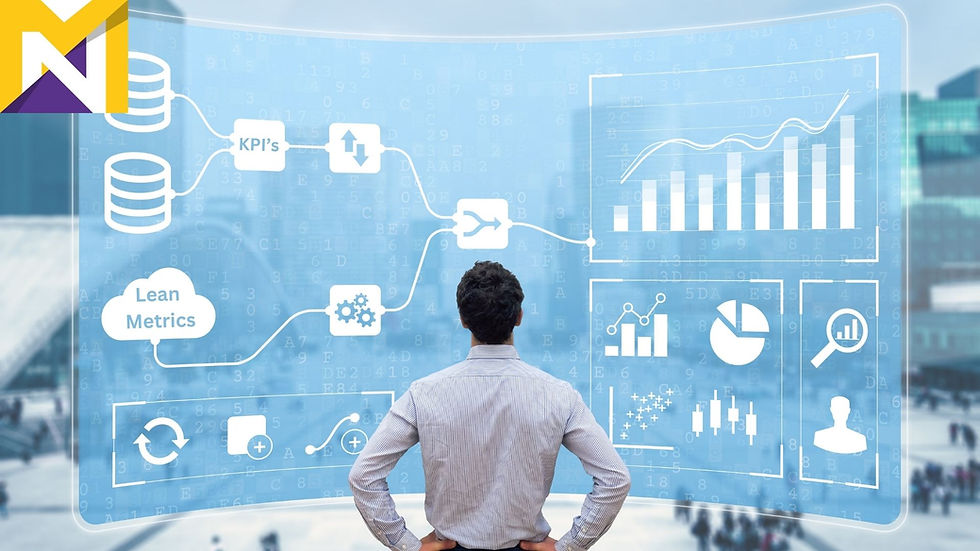
Organisations are constantly seeking ways to enhance their operational efficiency and deliver higher value to customers to maintain a competitive edge. In the manufacturing sector, Lean methodologies pave the way for sustainable growth.
Lean principles, originally developed by Toyota, focus on eliminating waste, optimising processes, and fostering a culture of Continuous Improvement. Effectively implementing Lean requires businesses to measure progress with Lean metrics and key performance indicators (KPIs). But what are Lean metrics, and how can they ensure business alignment to meet goals?
Defining relevant lean metrics
What are and why do they matter in Lean methodology?
Metrics are quantifiable data points used to assess the performance of processes, teams, and the organisation overall. Lean metrics serve as a compass, guiding efforts toward reducing waste, increasing efficiency, and improving quality.
To begin, organisations should identify and define the most relevant Lean metrics. These should align with the business’s specific goals and objectives.
Commonly used Lean metrics include:
Lead time: Reducing the time it takes to complete a process from start to finish is a fundamental Lean goal
Cycle time: Shortening the time it takes to complete one cycle of a process or production run reduces waste and improves responsiveness
Throughput: Increasing the rate at which products or services are produced or delivered helps meet customer demands efficiently
Defect rate: The percentage of products or services that do not meet quality standards
Work-in-progress (WIP): The number of unfinished tasks or products in the pipeline – lowering WIP streamlines workflows and reduces inventory costs
Customer satisfaction: Measuring customer feedback and satisfaction levels indicates the success of Lean improvements in delivering value to customers
Employee engagement: Engaged employees are more likely to embrace Lean principles and contribute to Continuous Improvement efforts
Cost of poor quality (COPQ): Calculating the cost associated with defects and rework provides insights into potential savings through quality improvements
By carefully selecting and defining these metrics, organisations can create a baseline for evaluating their current performance and identifying areas for improvement.
Monitoring and evaluating KPIs
Key performance indicators (KPIs) are specific metrics used to assess progress toward strategic goals. In the context of Lean, KPIs help organisations track the success of Lean initiatives and ensure they contribute to the overall business objectives.
To effectively monitor and evaluate KPIs in a Lean environment:
Establish a system for collecting data on the selected Lean metrics consistently and accurately to provide a clear picture of performance
Use visual tools like dashboards, scorecards, or Kanban boards to display KPIs in real time to stay focused on goals and foster transparency
When KPIs fall short of targets, conduct a root cause analysis (e.g. using the 5 Whys) to identify the underlying issues
Lean is all about Continuous Improvement, so adjust strategies and tactics based on KPI data to drive ongoing enhancements in processes and performance
Recognise and celebrate achievements when KPIs meet or exceed targets – positive reinforcement can boost team morale and motivation
Aligning metrics with business goals
Misalignment between Lean metrics and business objectives can lead to wasted efforts and resources.
So, to ensure business alignment:
Clearly articulate the business goals you want to achieve, whether it’s cost reduction, increased customer satisfaction, or improved competitiveness
Choose Lean metrics that directly support your business objectives – for instance, if cost reduction is a primary goal, focus on cost-per-unit metrics
Continuously assess whether your chosen metrics are still in sync with the evolving needs and goals of the business and adjust as necessary
Cascade metrics and KPIs throughout the organisation, from leadership down to frontline teams – everyone should understand how their work contributes to the larger business objectives
Example of cascade metrics
A manufacturing company called PrecisionTech is implementing Lean principles to enhance its operations and improve overall efficiency. Their key business objective is to reduce production lead time – but they need to cascade metrics throughout the organisation to ensure effective improvements within the business.

Here’s how…
Leadership level
At the leadership level, PrecisionTech’s executives aim to reduce production lead time by 20% within the next year – defining a specific KPI. The leadership team communicates this goal and KPI to the entire organisation during strategy meetings and updates.
KPI: Percentage reduction in production lead time
Target: 20%
Middle management level
Middle managers, responsible for various departments within the organisation (e.g., production, quality control, logistics), receive the directive from the leadership team.
They then break down the lead time reduction goal into department-specific KPIs.
Production Department KPI: Cycle time reduction in production line A
Target: 25% reduction
Quality Control Department KPI: Defect rate reduction in quality inspections
Target: 15% reduction
Logistics Department KPI: Inventory turnover improvement
Target: 10% increase
These departmental KPIs align with the overall goal to reduce lead time and are communicated to respective department heads.
Frontline teams
At the frontline level, teams within each department receive specific tasks and responsibilities tied to the departmental KPIs. For example:
Team A, responsible for a particular production line, works on process improvements to reduce cycle time to meet the 25% target.
Team B in the Quality Control Department focuses on enhancing inspection processes to reduce defects to meet the 15% target.
Team C in the Logistics Department emphasises efficient inventory management, ensuring that all team members understand the importance of the 10% turnover increase target.
PrecisionTech has effectively cascaded metrics and KPIs throughout the organisation. Every employee, from the leadership team to frontline workers, understands their role in achieving the overarching objective of reducing production lead time. Everyone works collectively towards the same goal, fostering a culture of Continuous Workflow Improvement and contributing to the company’s success in implementing Lean principles.
Continuous Improvement with Manufacturers Network
Lean metrics and key performance indicators provide organisations with the means to measure progress, identify areas for improvement, and align efforts with strategic business goals.
By carefully defining relevant metrics, monitoring KPIs effectively, and aligning with business objectives, organisations can achieve sustainable growth and Continuous Improvement. In turn, Lean principles and metrics-driven decision-making can drive efficiency, reduce waste, and enhance customer satisfaction – positioning businesses for success in today’s competitive landscape.
If you would like to learn more about Lean metrics and KPIs or to sign up for one of our courses, please contact us: